Better environments, inside and out.
Elevate your comfort, lower your impact
Get more efficiency
Reduce the amount of energy needed to heat and cool your home. Our heat pumps are between 160-390% more efficient than gas-burning furnaces.*
Save with credits and incentives
The federal Inflation Reduction Act (IRA) offers up to $2,000 in tax credits for qualified heat pump systems. Credits can be combined with local and utility incentives for huge savings.
Use less energy
According to U.S. Department of Energy, today's heat pumps can reduce your electricity use for heating by about 65% compared to electric resistance heating such as furnaces and baseboard heaters.**
No greenhouse gas emissions
Our all-electric systems do not produce carbon dioxide (CO2) or other greenhouse gases.
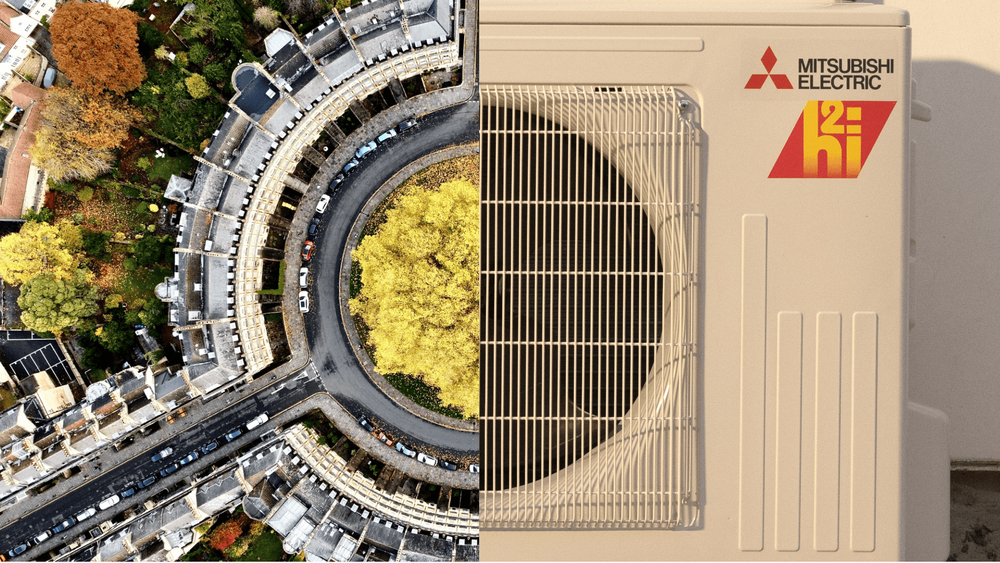
Our products
Explore our range of products for heating and cooling individual spaces in your home.
Electrify your home's HVAC, your way
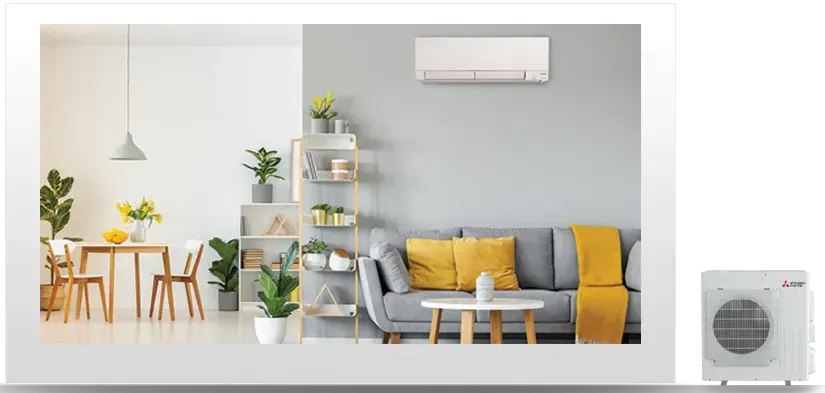
Single-zone
One outdoor unit connects to one indoor unit. This is ideal if you want to add heating or cooling control to a single space, which can be as small as a bedroom or as large as an entire floor in your home.
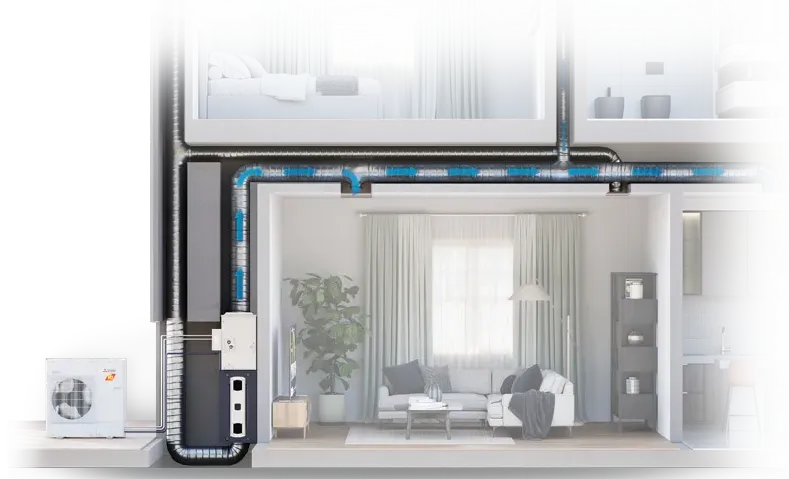
Hybrid HVAC
Compatible with most gas furnaces, the intelli-HEAT® dual fuel system cools and heats your home with electricity until gas heating is necessary, reducing gas usage and CO2 emissions.
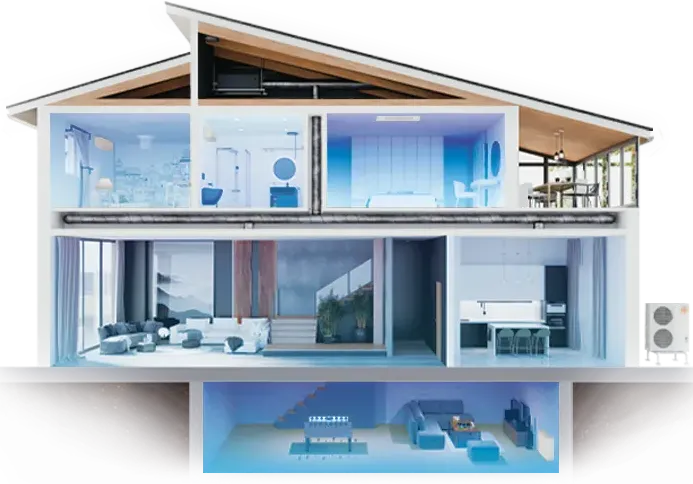
Whole home
Connect up to eight indoor units to one outdoor unit to create individually controlled zones, or upgrade your gas furnace for an air-handler and go all-electric while using your existing ducts.
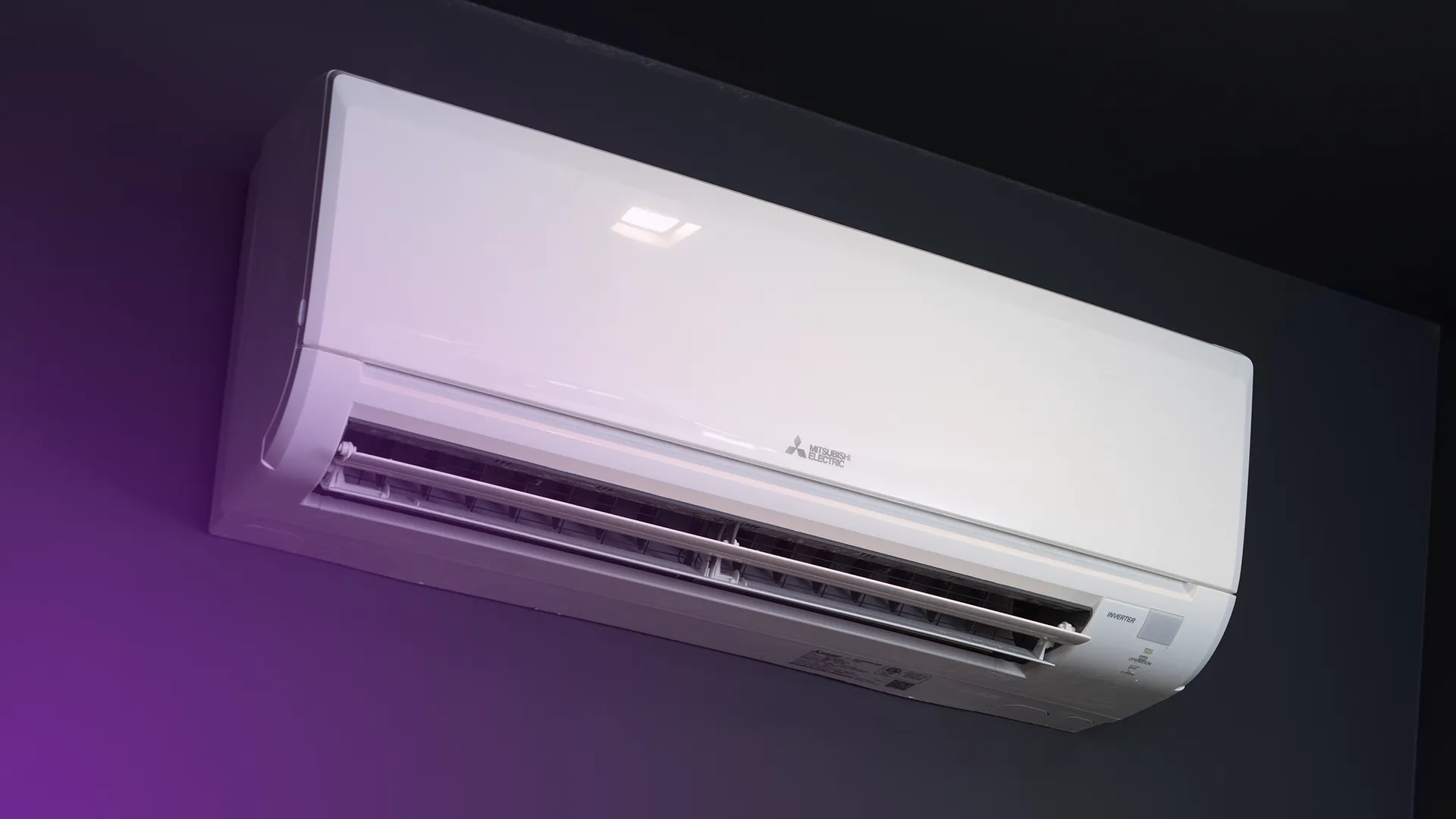
Take advantage of unprecedented federal energy efficiency improvement incentives
The Inflation Reduction Act of 2022
The largest ever climate investment by the Federal Government in American history. This energy relief bill incentivizes the adoption of efficient, all-electric appliances, like our heat pumps.
Heat pumps in the news
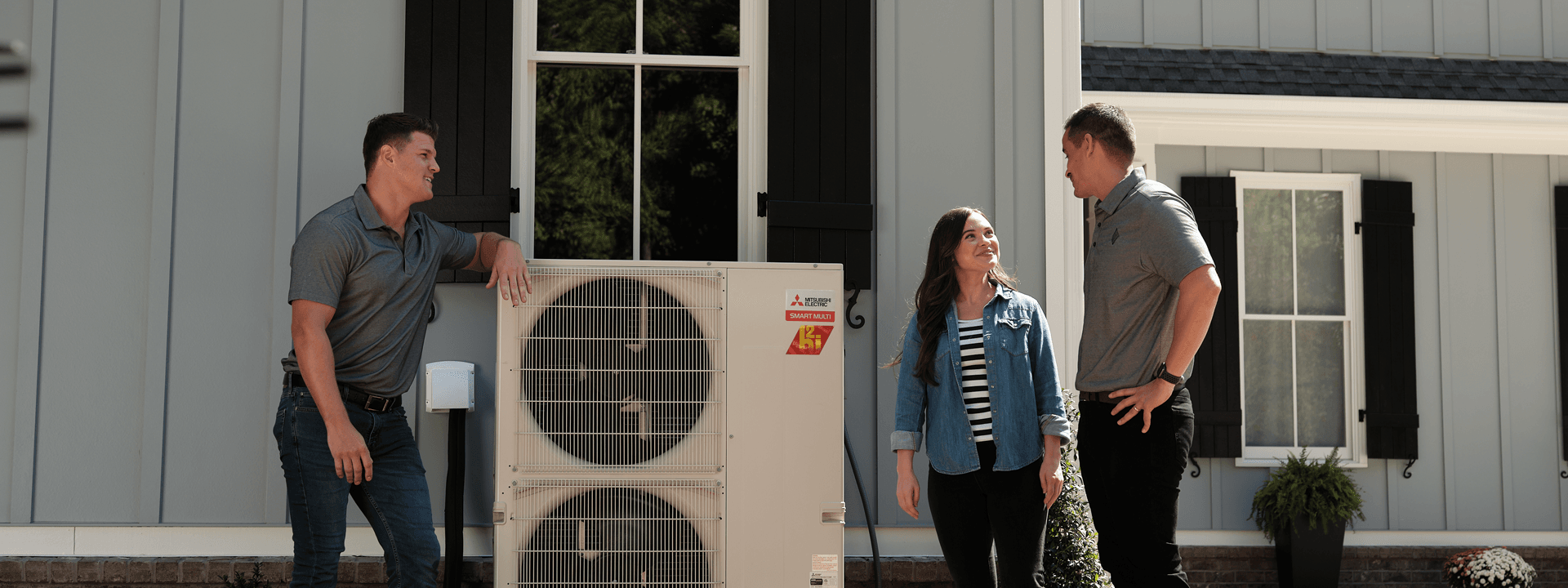
*Efficiency rating for each of our current heat pump models are located here and reflect the heat pump model’s COP. ”Efficiency” or “efficient” means that the heat pump delivers that amount more energy (in the form of heat) than the heat pump consumes in electricity. COP (coefficient of performance) is a measure of energy efficiency, with a higher efficiency associated with a higher COP. A COP of 1 is equivalent to 100% efficiency and a COP of 2 is equivalent of 200% efficiency (that is, it delivers twice that amount more energy in the form of heat than it consumes in electricity). Our “heat pump systems” are comprised of connected current models of Mitsubishi Electric outdoor and indoor heat pump units. COP rating testing was performed at 47° F, the industry standard. Furnaces can only, at their theoretical best, achieve 100% efficiency, or a COP of 1. Therefore, our heat pump systems, which have a COP of at least 2.6, have a COP of more than 1.6 that of gas-burning furnaces (which have at most a COP of 1) and are 160% more efficient.
**According to the U.S. Department of Energy, today's heat pump can reduce your electricity use for heating by approximately 65% compared to electric resistance heating such as furnaces and baseboard heaters.